Protect Your Crew and Your Bottom Line with a Hassle-Free Managed Safety Footwear Program.
Build your custom work safety shoe program with Shoes For Crews®,
a safety shoe distributor with industry leading slip resistance and full foot protection.
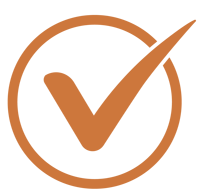
Improve Safety Culture
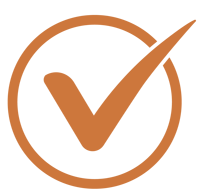
Reduce Slip & Fall Expenses
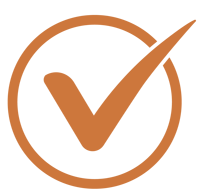
Simplify Program Management
Providing Superior Protective Footwear Couldn’t Be Easier.
Your crew may not be getting the protection they need from their current work safety shoes. Reduce up to 80% of expensive slip and fall accidents with our hassle-free safety footwear program and proprietary outsole technology.
Trusted By
A Complete Safety Footwear Solution —
Managed For You.
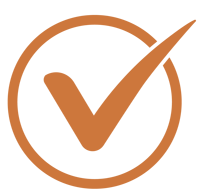
Save time and resources,
achieve safety goals.
Eliminate the hassle of managing your own program.​ Your dedicated Shoes For Crews team provides the support you need,from start to finish, with a hands-on approach.
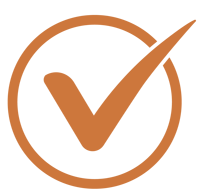
Convenient online tools,
all in one place.
Account management, data and reporting, payment and billing, marketing support, and online portal for easy ordering for your whole crew. Safety resources at your fingertips.
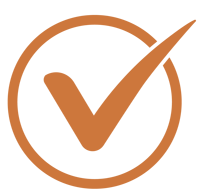
Industry-leading footwear
solutions you can trust.
As a trusted safety shoe distributor, our safety footwear exceeds the most stringent standards in slip resistance across the nation, with proprietary slip-and-oil resistant outsole technology.
Trusted Leader in Safety for More Than 35 Years
Over 30 years ago, Founder Stan Smith noticed a rise in workplace injuries caused by slip and falls. He made it his mission to solve the problem by developing safer shoes. Today, Shoes For Crews is the industry standard and trusted leader in safety footwear solutions for more than 150,000 companies around the world.
Proudly Serving Corporate Teams and Small Businesses
Around the World
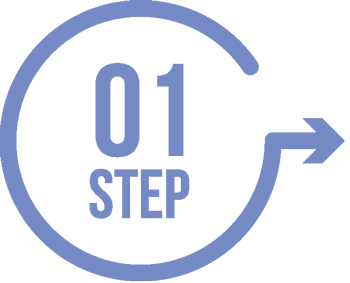
Get Started
We’ll assess your needs and design a fully-managed corporate safety footwear program that fits your company’s needs and goals — so you can protect your team and build a strong safety culture without the hassle.
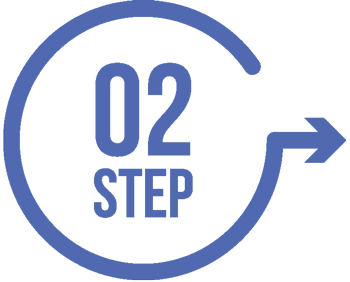
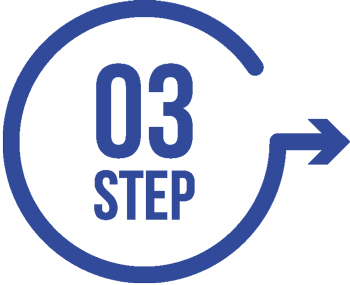
Maximize Workplace Safety
Now your team can select industry-leading safety footwear that reduces up to 80% of slip and fall accidents. And you protect your company, employees and profits from the devastating costs of workplace accidents.
Checklist
5 Signs You Need a Workplace Safety Program
A workplace safety program creates an established guideline to protect employees from potential dangers, improve bottom-line costs and strengthen your company’s safety culture.Don’t ignore these 5 signs that your company needs a custom safety shoe program!
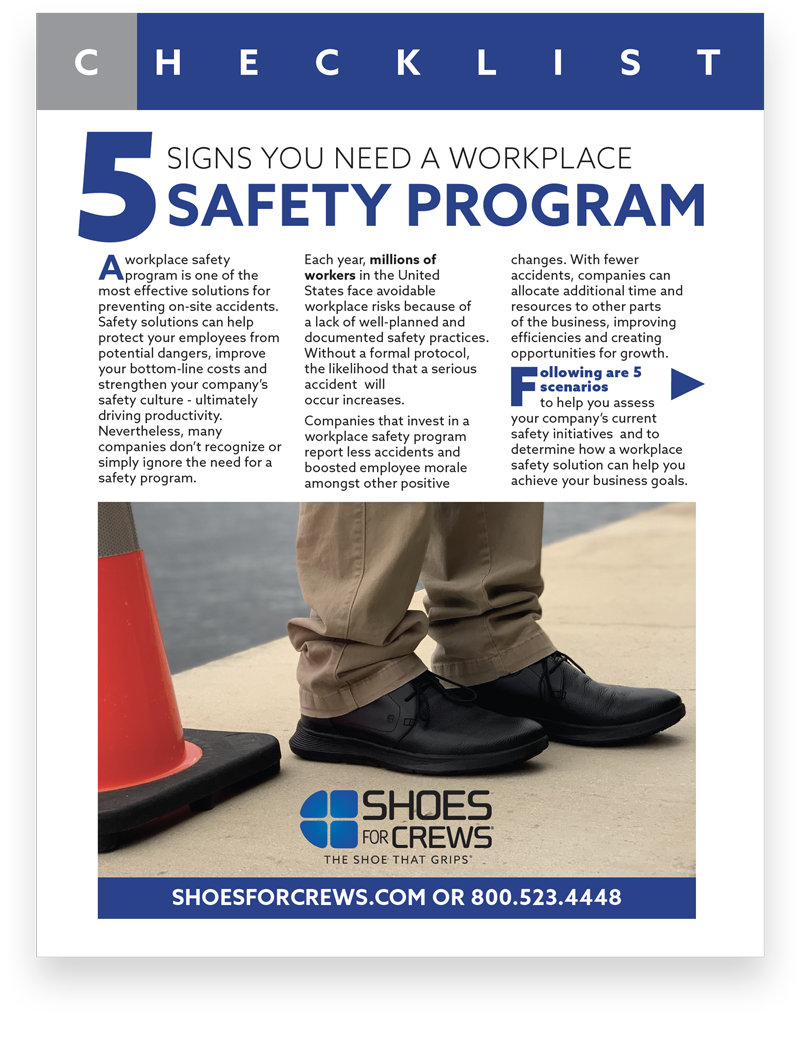
Let’s Get Started
Don’t get caught slipping! Speak with our experts about your safety footwear program needs.
Want Safety Resources At Your Fingertips?
Get Industry-Leading Safety Resources, Tips And Best Practices Delivered To Your Inbox!